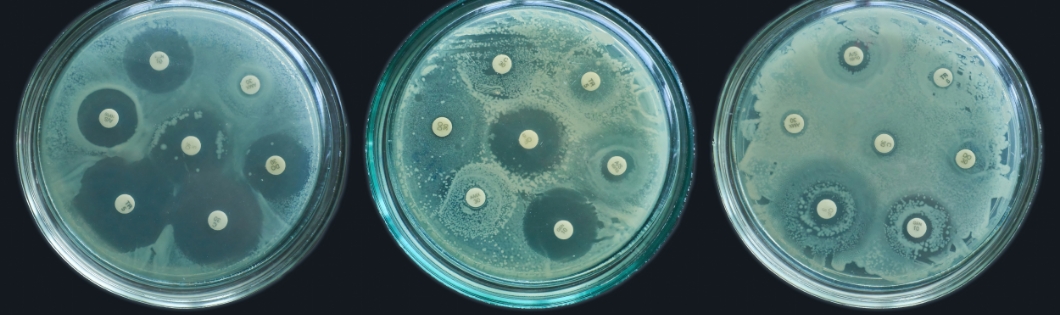
What Is a Cleanroom?
A cleanroom is a controlled, sterile environment where contaminants like dust, airborne microbes and aerosol particles are filtered out to provide the cleanest area possible. Besides filtering out contaminants, cleanrooms also control variables like temperature, air flow and humidity.
Cleanroom Requirements: 3 Factors That Must Be Regulated
With consumer and employee safety on the line, it is essential that your cleanroom adheres to the most up-to-date Good Manufacturing Practice (GMP) cleanroom standards from the FDA. There are three things that must be regulated in order to meet cleanroom requirements.
1. Internal Surfaces
All surfaces in a clean room must be smooth and impervious to microorganisms. In addition, they should be easy to clean and strong enough that they will not easily crack or shatter. Also, to meet cleanroom standards, surfaces should not create their own contamination, like dust. Suitable materials for internal surfaces can include glass – the top choice for many cleanrooms – or for a cheaper option, plasterboard with an epoxy coating.
2. Air Flow
Cleanrooms require a lot of air with regulated humidity and temperature. To meet cleanroom specifications, your air handling system must be strong enough to effectively deliver fresh, recirculated air into the cleanroom at a rate that will flush any particulate contamination out of the room. Filters built into cleanroom designs can remove particulates and other contaminants like moisture before the clean air is pumped back into the cleanroom.
3. Employee Access
The most effective way of maintaining the air quality in a cleanroom is to operate and maintain it correctly. The largest source of contamination in any cleanroom is people. That’s why you need to limit the number of people allowed in the room to only the specially trained personnel required to be in the room.
Cleanroom Standards and Classifications
International Organization for Standardization (ISO) guidelines are used for cleanroom classification. There are nine classes used to rate the cleanliness of a cleanroom, with a Class 1 facility having the most stringent specifications for maximum allowable contaminant concentrations, and a Class 9 facility permitting the highest level of contaminants. For example, a Class 1 cleanroom allows less than 2 particles larger than 0.3 microns and no particles greater than 1.0 microns per cubic meter.
Cleanroom classification is usually mandated by government regulations or industry standards.
Each class has specific cleanroom design standards that must be maintained in order to achieve official cleanroom certification. Factors considered include filter efficiency, air change rate, ceiling type, wall type, flooring cover and air returns.
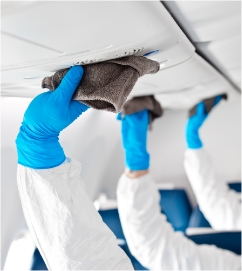
Let Duracote Help You Meet Your Cleanroom Requirements
Duracote is a leader in developing engineered materials that provide superior protection in cleanroom environments. Our DURA-STAT is a high-performance material that protects against static discharge and provides an ESD-safe environment thanks to its anti-static design, making it the perfect solution for medical, military, and pharmaceutical cleanrooms. Its unique multi-layer construction is durable and easy to fabricate, and DURA-STAT is resistant to flame and long-term wear.
Contact us today to find out more about how our Dura-Stat materials can help your facility meet cleanroom standards.