Understanding the Importance of Aerospace Interiors
Aerospace interiors, though often overshadowed by the marvel of aviation technology and aerodynamics, play a pivotal role in the overall aviation experience. Their importance is twofold, balancing both functionality and aesthetics.
Safety and Comfort
At the very heart of aerospace interiors lies the responsibility of safeguarding passengers. Every material chosen, every design implemented, and every fixture installed contributes to the overall safety of the aircraft’s occupants. From flame-resistant materials to those that can withstand sudden pressure changes, aerospace interiors are designed to be the first line of defense in various emergency scenarios. Furthermore, these interiors are crafted to ensure passenger comfort during flights, whether it’s a short domestic hop or a transcontinental journey. Proper insulation, vibration absorption, ergonomic design, and more come together to make air travel a seamless experience.
Design Aesthetics and Branding
Beyond safety and comfort, aerospace interiors serve as a canvas for airlines to express their brand identity. It’s the interiors that passengers interact with directly—seats, overhead compartments, lavatories, galley, and the ambient environment. A well-designed interior can elevate the passenger’s experience, creating a lasting impression and promoting brand loyalty. Airlines often collaborate with designers to infuse cultural motifs, innovative layouts, and luxury elements, making each flight memorable.
In essence, aerospace interiors are more than just a passive backdrop—they are active contributors to the aircraft’s operation, passenger safety, comfort, and the overarching brand experience. As the aerospace industry continues its ascent, the interiors will undoubtedly take center stage, underscoring the need for impeccable materials that rise to the occasion.
Key Aerospace Material Specifications
When it comes to the aerospace industry, material choices aren’t just about aesthetics or comfort. They’re deeply entrenched in an intricate web of specifications that determine the safety, durability, and functionality of the aircraft. Industry giants Boeing and Lockheed Martin have their own specifications to ensure that their products meet industry standards. Understanding aerospace material specifications is paramount in ensuring both compliance with global standards and the creation of products that stand the test of time.
An Overview of Standard Aerospace Material Specifications
NTF materials are designed to be durable and resistant to wear and tear. They can withstand heavy foot
traffic and exposure to chemicals and other substances, making them ideal for use in aircraft.
- Flammability: Given the closed environment of an aircraft, materials must resist combustion and limit the spread of flames. Specifications often mandate that materials self-extinguish within seconds when exposed to open flames.
- Flammability specifications for aircraft interior materials include the vertical burn, FAR25.853(a), the radiant panel, FAR 25.856(a), and flame penetration or “burn-through,” FAR25.856(b).
- Weight and Strength: In aviation, every gram counts. Materials need to be lightweight to enhance fuel efficiency, but without compromising on strength. This balance ensures the aircraft can carry significant loads without undue strain on its structure.
- Environmental Resistance: Aircraft interiors are exposed to a range of environmental conditions, from the cold at cruising altitudes to the heat of sun-exposed tarmacs. Materials should maintain their integrity and appearance despite these fluctuations.
- Chemical Resistance: With frequent cleaning and exposure to various substances, including jet fuel and deicing fluids, materials should resist chemical degradation.
The Balance Between Durability, Weight, and Performance
It’s a delicate dance. Aerospace materials must maintain a challenging trifecta—being robust enough to last, light enough to be economically viable, and performative enough to meet operational requirements. This balance is especially crucial for interiors, where passengers directly experience the material choices. Durability ensures interiors remain pristine over multiple flights; weight affects the aircraft’s efficiency and operating costs, and performance impacts passenger safety and comfort.
In sum, aerospace material specifications aren’t mere guidelines—they’re the backbone of every decision in the aerospace interior realm. Adhering to them ensures that the aircraft doesn’t just look good but operates at its peak, ensuring safety, efficiency, and a memorable passenger experience.
Qualities of a Reputable Aerospace Material Developer
When embarking on the quest to find an aerospace material developer, it’s not just about choosing a company that meets industry standards. It’s about aligning with a partner that stands head and shoulders above the rest. So, what sets a reputable developer apart from the pack?
Track Record in the Industry
Having an established history is a key marker to watch for. There’s something to be said for time-tested experience. Developers who have weathered the evolving tides of the aerospace industry often bring a wealth of knowledge to the table. Their longstanding presence can be an indicator of consistent quality and reliability.
While longevity is commendable, the aerospace industry is also ripe for innovation. Some newer entrants bring cutting-edge technologies and fresh perspectives. It’s essential to recognize and evaluate the potential of these trailblazers.
Certifications and Compliance with Global Standards
Quality isn’t just a buzzword in aerospace; it’s a non-negotiable. Reputable developers will possess certifications that prove their materials meet or exceed global aerospace material specifications. Look for affiliations with recognized industry bodies, certifications from relevant authorities, and a history of adherence to stringent quality checks.
Continuous Research and Development Initiatives
The aerospace industry isn’t static; it’s in constant flux, adapting to new technologies, regulations, and consumer demands. A leading aerospace material developer will invest heavily in R&D, consistently seeking to innovate and improve. Whether it’s developing more sustainable materials, enhancing durability, or finding ways to reduce weight without compromising strength, these R&D efforts are the lifeblood of forward-thinking developers.
Choosing an aerospace material developer is a decision of significant magnitude. It requires a deep dive into their history, an understanding of their commitment to quality, and an appreciation for their vision of the future. Aligning with a developer that embodies these qualities ensures that the materials chosen are not only of the highest caliber but are also poised to meet the challenges of tomorrow’s aerospace industry.
Navigating the Aerospace Material Developer Selection Process
Choosing the ideal aerospace material developer is akin to finding the perfect puzzle piece – it must be a seamless fit with your company’s ethos, needs, and future plans. However, navigating the vast sea of potential partners can be daunting. By following a systematic approach and knowing which aspects to prioritize, the selection process becomes more manageable and ensures a decision backed by informed judgment.
Evaluating the Manufacturer’s Portfolio
A developer’s portfolio is a window into their capabilities. Examine the range of materials they offer and look at their diversity and innovation. Do they cover a broad spectrum, catering to diverse aerospace needs? Furthermore, are there signs of innovation – materials that push boundaries or offer solutions to long-standing industry challenges?
Real-world application is another litmus test for any developer. The true test of any material is its performance in real-world conditions. Delve into case studies or examples of where and how the developer’s materials have been used. This not only validates the material’s efficacy but also showcases the developer’s reach in the industry.
Assessing Customer Testimonials, Reviews, and Case Studies
Feedback from previous clients is an invaluable resource. It offers insights into the developer’s professionalism, quality consistency, after-sales support, and more. While glowing testimonials are good, also look for instances where issues arose and how the developer handled them. This gives a clearer picture of their commitment to customer satisfaction.
Understanding Supply Chain Reliability and Responsiveness
In the aerospace industry, timelines are often tight, and there’s little room for delays. Therefore, understanding the reliability of the developer’s supply chain is crucial. Do they have a history of meeting delivery timelines? How do they handle unforeseen disruptions? Additionally, gauge their responsiveness. A developer who’s quick to address queries or concerns is likely to be a more dependable partner in the long run. The journey to selecting the perfect aerospace material developer is both a science and an art.
While objective metrics, past performance, and certifications play a significant role, one must also factor in subjective elements such as alignment with company values and vision. By adopting a holistic approach, you ensure that the partnership forged is both productive and enduring.
Frequently Asked Questions About Aerospace Interiors & Material Developers
If you have questions about aerospace interior materials, we are happy to help. That’s why we have answered a few common questions we hear below.
What Are the Advanced Materials Used in the Aerospace Industry?
In the aerospace industry, advanced materials play a crucial role in enhancing performance, safety, and fuel efficiency. These include:
- Composites: These are materials made from two or more constituent materials with significantly different physical or chemical properties. Commonly used composites in aerospace include carbon fiber-reinforced polymers (CFRPs) and glass fiber-reinforced polymers (GFRPs).
- Titanium Alloys: Renowned for their strength and lightweight, titanium alloys are often used in aircraft structures and engines.
- Advanced Ceramics: These are used in parts that need to resist high temperatures, such as engine components.
- Aluminum Alloys: Still widely used in the aerospace industry, they offer a good balance of strength, corrosion resistance, and weight.
- Polymer Matrix Composites (PMCs): These are composed of a variety of short or continuous fibers bound together by an organic polymer matrix. They’re prized for their weight-saving properties.
How Are Aircraft Advanced Composite Materials Manufactured?
The manufacturing of aircraft advanced composite materials involves a series of precise and controlled steps:
- Lay-up Process: This is the most common method, where layers of fibrous materials (like carbon or glass fibers) are stacked and then infused with a resin
- Curing: Once the layers are stacked, they undergo a curing process, typically under heat and pressure, in an autoclave, which solidifies the resin and binds the fibers together.
- Prepreg: Another method uses prepreg, which is a pre-impregnated composite fiber material (like carbon fiber) that already contains the resin. It’s laid up in molds and then cured.
- Resin Transfer Molding (RTM): In RTM, dry fibers are placed in a mold, and then resin is injected to impregnate the fibers, followed by the curing process.
- Filament Winding: For cylindrical components like tanks or pipes, continuous reinforcing fibers are soaked in resin and then wound around a rotating mandrel in a predetermined pattern.
Advanced machinery, quality control measures, and skilled technicians ensure the materials produced meet the high standards required for aerospace applications.
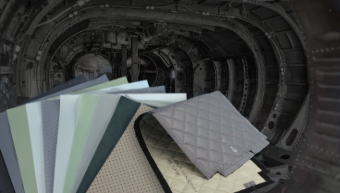
Ready to Elevate Your Vision for Aerospace Interiors? Trust Duracote
Transforming the future of aerospace demands more than just ambition – it requires the right partners, materials, and insights. With every decision, you have the power to shape what tomorrow looks like in the skies. Explore the expertise of a top-tier aerospace material developer like Duracote, and let our legacy guide your path. Our experienced team of developers creates unique custom advanced materials solutions for the aerospace industry and other applications. Are you ready to champion the next wave of aerospace innovation? Connect with the experts today and let your vision take flight.