What Matters Underfoot: Core Specs That Define Aircraft Flooring Performance
When specifying an aircraft flooring material, success lies in aligning material characteristics with operational realities. Every decision needs to align with aviation-grade engineering standards, cabin usage profiles, and the operational priorities of the fleet.
The following criteria form the core decision matrix for aerospace manufacturers and suppliers evaluating aircraft flooring options.
Regulatory & Safety Compliance
All flooring material must comply with Federal Aviation Regulation (FAR) 25.853(a), which governs flammability in aircraft cabin interiors. Materials must also meet criteria for low smoke emissions, non-toxic gas release, and thermal stability.
Durability & Wear Resistance
Aircraft flooring takes a daily beating from service carts, luggage, high heels, rolling bags, and rapid clean cycles. Materials must resist:
- Abrasion from rolling carts
- Indentation under heavy static loads
- Impact from dropped service items
- Chemical exposure from sanitizers and solvents
Weight & Fuel Efficiency
In aerospace design, weight isn’t just a number—it’s a fuel bill. Flooring contributes to total aircraft weight, so every ounce saved translates to measurable performance gains.
Installation & Maintenance
Downtime is expensive. That’s why fast, simple installation and easy field maintenance are essential. Duracote’s aircraft vinyl flooring systems are available in formats that support:
- Quick laydown and bonding
- Removable options for field rework
- Stain-resistant surfaces for faster cleaning
- Cut-to-fit design flexibility for complex cabin layouts
When flooring materials are easier to install, inspect, and replace, entire fleet maintenance programs benefit from lower long-term costs.
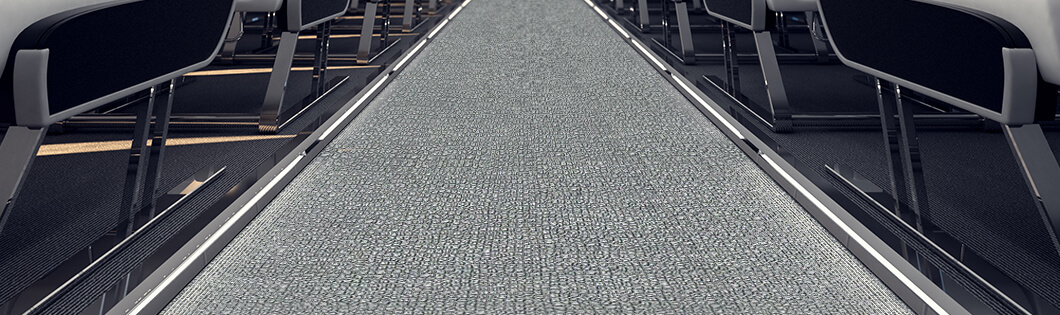
Inside the Build: How Duracote Floors Are Engineered to Outlast
Knowing which aircraft flooring material you need begins with understanding how it’s constructed—layer by layer—and what it’s engineered to withstand. Here at Duracote, our lineup isn’t broad for the sake of variety. It’s targeted: two core systems, each for specific roles inside an aircraft cabin, differentiated by performance thresholds, material makeup, and install configurations.
Both options—NEXFLOR® and DURUG®—are classified as non-textile flooring (NTF) and meet FAR 25.853(a) for flame resistance. Beyond that, their divergence begins in structure, underfoot behavior, and lifecycle intent.
NEXFLOR® | Precision-Tuned Aircraft Vinyl Flooring
NEXFLOR® is Duracote’s advanced, lightweight aircraft vinyl flooring system designed for commercial, regional, and business jet interiors.It combines multi-layer composite construction with precisely engineered surface treatments to deliver a flexible, high-performing floor solution across a range of cabin environments.
Construction profile:
- Multi-layered vinyl composite with an embedded anti-static wear layer.
- Standard thickness: ~0.045”
- Nominal weight: ~12–14 oz/yd²
- Slip coefficient: 0.6 (dry); coin dot variant offers higher traction.
Material behavior:
- Excellent dimensional stability during thermal cycling.
- Formable across curves and steps, suited for custom floorplan geometries.
- Offers chemical resistance to typical cabin cleaning agents and spills (quats, alcohols, glycol-based deicers).
Options:
- Surface textures: smooth matte, embossed, or coin dot.
- Visuals: tonal solids, faux woodgrain, stone, and metallic series.
- Pressure-sensitive adhesive or heat-bond installation systems available.
Why it works: NEXFLOR® is a low-weight, fast-install material built for cabins where cosmetic fidelity and compliance aren’t optional.It flexes (literally and logistically) where modularity matters.
DURUG® | Load-Bearing Coin Dot Flooring with Underlay Options
For heavy-duty aerospace and defense applications, DURUG® offers rugged performance with layered construction and underlay options tailored for shock absorption and sound deadening.Its coin dot surface adds slip resistance and tactile feedback for crew and passenger zones with dynamic movement.
Construction profile:
- Top layer: rigid-wear polymer bonded to a vinyl base.
- Available with or without closed-cell foam underlay (1/8″ or 1/4″).
- Total system thickness: Up to ~0.310″ depending on configuration.
- Weight range: Heavier than NEXFLOR®; varies by underlay spec.
Material behavior:
- Highly resistant to compression set and impact deformation.
- Underlay foam provides shock absorption and sound deadening.
- Maintains structural integrity under service carts, loading gear, and repeated point loads.
Options:
- Textured coin dot surface standard.
- Color schemes: mono-tone, two-tone, or tri-tone with custom color-matching.
Why it works: DURUG® is a tactile, overbuilt flooring system for areas that get hit harder, loaded heavier, or ignored less.It’s not aesthetics—it’s about longevity under strain.
NEXFLOR® vs. DURUG®: Side-by-Side Specs for Smarter Selection
When you’re narrowing down flooring systems, the spec sheet often makes or breaks the decision. Below is a side-by-side breakdown of our two primary aircraft flooring solutions —NEXFLOR® and DURUG®—highlighting the most critical variables in aerospace flooring selection.
Specification | NEXFLOR® | DURUG® |
---|---|---|
Material Type | Multi-layered aircraft vinyl composite | Reinforced wear-layer with optional foam underlay |
Thickness (Nominal) | ~0.045″ (1.1 mm) | 1/8″ or 1/4″ (with/without underlay) |
Weight | ~12–14 oz/ft² | Heavier; varies by configuration |
Surface Texture Options | Smooth matte, embossed, coin dot | Standardized coin dot texture |
Slip Resistance | High (≥ 0.6 dry); coin dot increases grip | Very high, especially with coin dot texture |
FAR 25.853(a) Compliant | Fully compliant | Fully compliant |
Electrical Resistance | Anti-static (≤10⁹ ohms surface) | Anti-static treated |
Installation Method | Pressure-sensitive or heat-bond adhesive | Standard adhesives; optional modular replacement |
Visual Design Options | Extensive (solids, woodgrain, stone, metallic) | Limited; solid or dual/tri-tone color schemes |
Best Use Case | Commercial, regional, and business interiors | Cargo, military, retrofit, high-impact zones |
Maintenance Behavior | Easy-clean surface; low scuffing | Rugged; resistant to compression and wear |
Acoustic/Impact Damping | Minimal | High (especially with foam underlay) |
Custom Fit for Curves | Excellent formability for complex layouts | Moderate; more rigid due to construction |
Fleet by Fleet: Matching Flooring Materials to Aircraft Roles
Choosing the best aircraft flooring material means matching the mechanical and environmental demands of each aircraft type and zone to the flooring’s structural behavior, lifecycle profile, and installation strategy.
Here’s a breakdown of how to choose between our NEXFLOR® and DURUG® based on real-world applications across fleet categories.
Commercial & Regional Passenger Aircraft
Passenger fleets face high turnover, tight maintenance windows, and the need for visual uniformity across models. Flooring must be fast to install, consistent across platforms, and light enough to meet fuel economy targets.
Recommended material: NEXFLOR®
NEXFLOR® offers the best blend of lightweight construction, non-slip protection, and aesthetic modularity. Coin dot variants add traction in front-of-cabin service zones, while smooth matte finishes provide a seamless visual across the passenger cabin. The ease of installation supports rapid turnaround during heavy maintenance cycles or interior refresh programs.
Best zones for deployment:
- Forward and aft entryways
- Lavatories and galleys
- Under-seat zones and aisleways
- Crew rest and service areas
Business Aviation & VIP Interiors
In business aviation, the visual and tactile feel of the floor is part of the experience. Materials must match interior styling, contour cleanly around custom floor plans, and still meet strict certification requirements.
Recommended material: NEXFLOR®
With its versatile aesthetic library—from woodgrains to brushed metallic patterns—NEXFLOR® integrates well into high-design custom cabins. The material’s low profile and excellent formability also simplify fit-out around hatch lips, seat mounts, and curved flooring features. It supports high-end branding without compromising regulatory adherence.
Best zones for deployment:
- Full cabin floor coverage (except cargo or utility zones)
- Lounges, lavs, and walkways
- Entry vestibules with design-matched inserts
Military, Cargo, and Utility Aircraft
Tactical and industrial aircraft demand rugged flooring that resists abuse from equipment, boots, and environmental extremes. Function takes priority over form, and field-replaceable solutions are often a necessity.
Recommended material: DURUG® (with underlay)
Military aircraft don’t need pretty—they need tough. DURUG®’s rigid polymer surface and optional foam underlay protect against compression set, puncture, and thermal fatigue. Its coin dot pattern provides aggressive surface grip even when wet, and its modular build supports full or partial replacement in field maintenance scenarios.
Best zones for deployment:
- Ramp entries and cargo doors
- Rear lavatories and service paths
- Structural load zones near tie-downs or troop seating
Mixed-Use or Retrofit Fleets
Not every operator runs a homogenous fleet—and not every interior needs a full strip and replace. Some aircraft benefit from using both flooring systems strategically to reduce cost and extend service life.
Recommended configuration: Mixed NEXFLOR® + DURUG®
You don’t need overbuilt flooring where it won’t get stressed. Many retrofit programs spec NEXFLOR® forward of the wing and reserve DURUG® for galley-to-ramp sections. This hybrid strategy simplifies procurement, minimizes weight in low-impact zones, and increases longevity where the flooring takes daily abuse.
Frequently Asked Questions About Aircraft Flooring Material
If you’d like to learn more about aircraft flooring material and its importance, check out our helpful FAQs down below for more insights.
What are the fire safety requirements for aircraft flooring materials?
Aircraft flooring must comply with FAR 25.853(a), which outlines flammability standards for cabin materials. Flooring systems are tested for vertical burn resistance, low smoke density, and minimal toxic gas emissions to ensure passenger and crew safety in emergency conditions.
Are there custom design options for aircraft flooring?
Yes—especially with systems like Duracote’s NEXFLOR®, which offers a wide range of colors, textures, and even woodgrain or metallic visual patterns. Custom color-matching and surface embossing (such as coin dot flooring) allow manufacturers to align flooring aesthetics with brand and cabin design requirements.
Why is lightweight flooring important for aircraft?
Every pound on board impacts fuel efficiency, payload capacity, and emissions. Lightweight flooring materials reduce overall aircraft mass, helping operators cut operating costs and improve performance margins without sacrificing durability or compliance.
Let’s Make the Right Choice for Your Fleet
Choosing the right aircraft flooring material is never just a design decision—it’s an operational one, with downstream effects on compliance, maintenance cycles, and overall fleet efficiency. Whether you’re outfitting a new platform, retrofitting high-traffic zones, or standardizing materials across aircraft classes, our proven aerospace flooring solutions are engineered to meet the spec—down to the gram, the micron, and the hour in service.
Contact us today to start a conversation about what your fleet needs—and what your flooring should be doing better.