Article Contents
Understanding Pressure-Sensitive Adhesives
Pressure-sensitive adhesives are a distinct category of adhesive tapes and substances that adhere to surfaces under light pressure.They are composed of elastomers, resins, and plasticizers to create a sticky, elastic surface. Unlike traditional adhesives that need heat, water, or solvents to activate, pressure-sensitive adhesives are inherently tacky at room temperature, allowing for immediate bonding upon application.
This form of adhesive is an integral part of products we encounter daily, from labels and tapes to medical devices and automotive trim. Their ease of use and versatility make them an indispensable tool in various applications. Duracote’s developmental products showcase innovative uses of these adhesives in cutting-edge applications, emphasizing their significance in modern manufacturing processes.
Pressure-Sensitive Adhesive vs. Contact Adhesive: Understanding the Differences
Understanding the difference between pressure-sensitive and contact adhesives is key to selecting the right adhesive for a particular application. While both are used to bond surfaces, their activation and bonding mechanisms differ significantly. Contact adhesives require the adhesive to be applied to both surfaces and allowed to dry before the surfaces are pressed together. In contrast, pressure-sensitive adhesives bond instantly to a surface with the application of light pressure.
The distinction lies in their chemical composition and physical properties. PSAs maintain a balance between flow and resistance, enabling them to adhere instantly but also be removable or repositionable in some cases. This makes them ideal for applications like temporary labels or protective films, where temporary adhesion is beneficial.
Duracote’s Dura-Trim Aviation Fire Safety and Durasonic Aviation Sound Control products exemplify the specialized use of PSAs in demanding environments, demonstrating how these adhesives perform under stringent safety and performance requirements.
Diverse Types of Pressure-Sensitive Adhesives
Pressure-sensitive adhesives come in various forms, each suited for specific applications.The main types of PSAs include:
- Rubber-based adhesives:Provide quick adhesion and are ideal for bonding to low-energy surfaces.
- Acrylic adhesives:Known for their excellent environmental resistance, suitable for outdoor applications.
- Silicone adhesives:Best for high-temperature applications and adhering to difficult surfaces.
Each type has unique properties that make it suitable for different applications, from the pressure-sensitive adhesive glue used in household items to specialized pressure-sensitive adhesives for vinyl flooring.
The Wide Range of Pressure-Sensitive Adhesive Applications
The versatility of pressure-sensitive adhesives extends across numerous industries. Let’s take a look at a few of the sectors where PSAs are widely used.
Aerospace
In the aerospace industry, PSAs play a crucial role. Duracote’s contributions to the aerospace sector, as seen in our compliance with Boeing and Lockheed Martin specifications, highlight the importance of reliable and high-performance adhesives in aircraft manufacturing and maintenance.
Consumer Products
Pressure-sensitive adhesives are used in everything from simple household tapes to complex automotive components. Their ability to bond to a variety of surfaces without the need for additional preparation or curing makes them a go-to solution for quick and effective adhesion.
Manufacturing
In the manufacturing sector, pressure-sensitive adhesives have become a vital component due to their efficiency and versatility. PSAs offer a quick and reliable method for bonding materials without the need for heavy equipment or extended curing times. This makes them ideal for use in assembly lines and automated processes, where speed and efficiency are paramount.
Transportation
The transportation industry relies heavily on PSAs for both construction and maintenance of vehicles, from cars and trucks to airplanes and trains. In automotive manufacturing, PSAs are used for a variety of purposes, including attaching interior trim, securing wire harnesses, and bonding insulation materials. Their resistance to temperature fluctuations and durability under stress make them ideal for use in environments subjected to constant vibration and varying weather conditions.
Composition and Characteristics of PSAs
The distinctiveness of pressure-sensitive adhesives lies in their composition, which grants them properties like instant tack and adherence under light pressure. The primary components of PSAs are:
- Elastomers:Provide the adhesive with flexibility and elasticity.
- Resins:Enhance the adhesive’s tackiness and bonding strength.
- Plasticizers:Improve the adhesive’s flexibility and help in lowering the viscosity.
This unique blend results in adhesives that are tacky at room temperature and capable of forming a bond with light pressure application, without the need for heat or moisture. Their viscoelastic nature allows PSAs to be strong enough to hold materials together yet flexible enough to allow for easy removal or repositioning when necessary.
Innovations in Pressure-Sensitive Adhesive Technology
Innovations in the world of pressure-sensitive adhesives are not just enhancing their existing capabilities but also opening new avenues for application.Some of the cutting-edge advancements in PSA technology include:
- Smart Adhesives:The integration of smart technologies into adhesives, enabling functionalities like temperature sensing and pressure responsiveness.
- Nano-enhanced PSAs:Utilizing nanotechnology to improve adhesive performance, particularly in terms of strength and durability.
- Development of Eco-friendly PSAs:With a growing focus on sustainability, the development of environmentally friendly PSAs using biodegradable materials is a significant step forward.
- Enhanced Durability:Modern PSAs are designed to withstand extreme conditions, such as high temperatures and humidity, making them suitable for challenging environments.
- Improved Adhesive Properties:Advances in chemical engineering have led to PSAs with better tack, shear resistance, and longer shelf life.
These technological leaps are propelling PSAs into the future, expanding their application scope far beyond traditional uses. Duracote’s Invent page showcases some of these groundbreaking developments, emphasizing our role in driving innovation in adhesive technology.
Frequently Asked Questions About Pressure-Sensitive Adhesives
How Does Pressure-Sensitive Adhesive Work?
Pressure-sensitive adhesives are unique in their ability to form a bond simply through the application of light pressure. They work based on the principles of viscoelasticity, which means they exhibit both viscous and elastic characteristics. When pressure is applied, the adhesive flows to cover the surface, creating a bond. This bond is strong enough to resist shear and peel forces, yet it can be peeled off easily without leaving residue, depending on the adhesive formulation.
PSAs do not require a chemical reaction to form a bond, differentiating them from other adhesive types. This property makes them highly versatile and suitable for a wide range of applications, from temporary notes to permanent automotive attachments. Duracote’s Durasonic Aviation Sound Control product line provides an excellent example of how PSAs are utilized in demanding and specialized applications.
What Is the Difference Between Pressure-Sensitive and Contact Adhesive?
The main difference between pressure-sensitive and contact adhesives lies in their method of application and bonding. Pressure-sensitive adhesives bond surfaces upon the application of light pressure and are ready to use immediately. In contrast, contact adhesives require both surfaces to be coated with adhesive, which then must dry before the two surfaces are pressed together to form a bond.
Contact adhesives are typically used for strong, permanent bonds, especially where high strength and resistance to temperature and solvents are needed. Pressure-sensitive adhesives, on the other hand, offer versatility for applications requiring temporary or repositionable bonds, as well as permanent bonding in various conditions. Duracote’s Dura-Trim Aviation Fire Safety products are a testament to the effectiveness of PSAs in critical safety applications.
Advanced machinery, quality control measures, and skilled technicians ensure the materials produced meet the high standards required for aerospace applications.
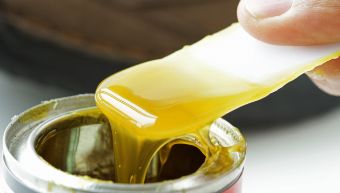
Trust Duracote’s Pressure-Sensitive Adhesives to Enhance Your Products
Are you looking to integrate cutting-edge adhesive solutions into your products? Whether your needs are in the realm of aviation, automotive, consumer goods, or beyond, Duracote’s range of pressure-sensitive adhesives offers the reliability, innovation, and performance you require.
Explore our developmental products to discover how our PSAs can revolutionize your applications. For tailored solutions and expert advice, contact us today. Let’s bond over innovation and shape the future together with Duracote’s advanced adhesive technologies.